Содержание
Виды соединений деталей. Резьбы, допуски и посадки
Виды соединений деталей
За долгие века своего развития человечество придумало множество способов соединения деталей. Деталью договоримся называть некий материальный объект, входящий в соединение, который не может быть разделен на более мелкие объекты. Соединение нескольких деталей условимся называть узлом, а совокупность узлов, способных при соединении выполнять определенные действия – механизмом.
Принято различать соединения деталей подвижные и неподвижные, В подвижных соединениях детали движутся друг относительно друга, а в неподвижных жестко скреплены друг с другом. Каждый из этих двух типов соединений подразделяют на две основные группы: разъемные и неразъемные.
Разъемными называются такие соединения, которые позволяют производить многократную сборку и разборку сборочной единицы без повреждения деталей. К разъемным неподвижным соединениям относятся резьбовые, штифтовые, шпоночные, шлицевые, профильные, клеммовые.
Неразъемными называются такие соединения, которые могут быть разобраны лишь путем разрушения. Неразъемные неподвижные соединения осуществляются механическим путем (запрессовкой, склепыванием, загибкой, кернением и чеканкой), с помощью сил физико-химического сцепления (сваркой, пайкой и склеиванием) и путем погружения деталей в расплавленный материал (заформовка в литейные формы, в пресс-формы и т. п.)
Подвижные неразъемные соединения собирают с применением развальцовки, свободной обжимки. В основном это соединения, заменяющие целую деталь, если изготовление ее из одной заготовки технологически невозможно или затруднительно и неэкономично.
Резьбовые соединения деталей являются наиболее распространенным видом разъемных соединений. Резьба – выступы, образованные на основной поверхности винтов и гаек и расположенные по винтовой линии. Несмотря на кажущуюся простоту резьбовые соединения весьма разнообразны. Поэтому в рамках текущего курса мы рассмотрим те из них, которые широко встречаются в нашем ассортименте. Но сперва дадим общую классификацию.
Резьбы, допуски и посадки
По форме основной поверхности различают цилиндрические и конические резьбы. Наиболее распространена цилиндрическая резьба. Коническую резьбу применяют для уплотняющихся и герметичных соединений труб, масленок, пробок и т.п.
По профилю резьбы различают треугольные, прямоугольные, трапецеидальные, круглые и другие резьбы.
По направлению винтовой линии различают правую и левую резьбы. У правой резьбы винтовая линия идет слева направо и вверх, у левой – справа налево и вверх. Наиболее распространена правая резьба.
По числу заходов – однозаходная и многозаходная резьбы. Наиболее распространена однозаходная резьба.
Резьбу получают (формируют) несколькими способами:
-
лезвийная обработка; -
накатывание; -
абразивная обработка; -
выдавливание прессованием; -
литьё; -
электрофизическая и электрохимическая обработка.
Наиболее распространённым и универсальным способом получения резьб является лезвийная обработка. К ней относятся:
Накатывание является наиболее производительным способом обработки резьб, обеспечивающим высокое качество получаемой резьбы. К накатыванию резьб относятся:
К абразивной обработке резьб относится шлифование однониточными и многониточными кругами. Применяется для получения точных, в основном ходовых резьб.
Выдавливание прессованием применяется для получения резьб из пластмасс и цветных сплавов. Не нашло широкого применения в промышленности.
Литьё (обычно под давлением) применяется для получения резьб невысокой точности из пластмасс и цветных сплавов.
Электрофизическая и электрохимическая обработка (например, электроэрозионная, электрогидравлическая) применяется для получения резьб на деталях из материалов с высокой твердостью и хрупких материалов, например твёрдых сплавов, керамики и т. п.
Рассмотрим теперь основные геометрические параметры цилиндрических резьб. Они включают: наружный d, средний d2 и внутренний d1 диаметры резьбы, шаг резьбы р, угол профиля α.
Метрическая резьба ISO – основной вид резьбы крепежных деталей с углом профиля α = 600. Широко употребима в Европе и Азии. Профиль – равносторонний треугольник со срезанными вершинами. Размеры указываются в миллиметрах.
Метрическая резьба бывает с крупным и мелкими шагами. Чаще всего, наиболее износостойкую и технологичную резьбу выполняют с крупным шагом. Резьбы с мелким шагом используются реже. Ниже приводится таблица, составленная на основании ГОСТ 8724-81 «Резьба метрическая. Диаметры и шаги».
Шаг резьбы для крупной и мелкой резьбы (однозаходной)
(Размеры в скобках действительны для новых стандартов ISO)
|
| |||
|
| |||
|
|
| ||
|
|
|
|
|
|
|
|
|
|
|
|
|
|
|
|
|
|
|
|
|
|
|
|
|
|
|
|
|
|
|
|
|
|
|
Кроме упомянутых выше основных характеристик существуют дополнительные: сбег, недорез и недовод.
Участок конечных витков резьбы, имеющих неполный профиль, называется сбегом резьбы. Сбег резьбы — участок неполного профиля в зоне перехода резьбы в гладкую часть детали, возникает при отводе режущего инструмента от изделия.
Недовод резьбы — величина ненарезанной части поверхности детали между концом сбега и опорной поверхностью детали (при переходе с одного диаметра на другой).
Недорез резьбы — участок поверхности детали, включающий сбег резьбы и недовод.
Величина недореза важна, например, при соединении двух тонких листов стали: при излишне большом недорезе соединение может быть неплотным.
Также встречаются также дюймовые резьбы нескольких видов (1 дюйм равен 25,4 мм).
Дюймовая резьба UTS, ISO 5864. Используется преимущественно в США. Профиль – равносторонний треугольник (угол при вершине 60о) со срезанными вершинами. При одном диаметре резьба может иметь крупный (UNC) или мелкий (UNF) шаг. Размеры резьбы указываются в долях дюйма и в числе витков, приходящихся на дюйм. Для маленьких диаметров резьбы перед числом витков через дефис ставится порядковый номер резьбы: от 0 до 12.
Дюймовая резьба Витворта BSW. Используется преимущественно в Великобритании. Профиль – равнобедренный треугольник (угол при вершине 55 градусов). При одном диаметре резьба может иметь крупный (BSW) или мелкий (BSF) шаг. Размеры указываются в долях дюйма и в числе витков резьбы на дюйм.
-
Дюймы
Номинал
мм
Число ниток
на дюйм UNC
Число ниток
на дюйм UNF
Номер-чн UNC
Номер-чн UNF
Чн
на дюйм BSW
Чн
на дюйм BSF
1,524
80
0-80
1,854
64
72
1-64
1-72
2,184
56
64
2-56
2-64
2,515
48
56
3-48
3-56
2,844
40
48
4-40
4-48
1/8
3,175
40
44
5-40
5-44
40
Классификация разъемных соединений.
Разъемные соединения деталей машин
Соединения деталей машин и механизмов, допускающие многократную разборку и сборку без повреждения соединяемых деталей и соединительных элементов называются разъемными соединениями. Разъемные соединения в свою очередь делятся на подвижные и неподвижные.
С помощью подвижных соединений можно обеспечить определенное перемещение одних деталей относительно других. К ним относятся различные опоры и направляющие.
Неподвижные соединения обеспечивают фиксированное положение одних деталей по отношению к другим.
К разъемным соединениям относят резьбовые, штифтовые, шпоночные, шлицевые и некоторые другие соединения. Выбор типа соединения зависит от предъявляемых к нему требований: конструктивных, технологических и экономических.
***
Резьбовые соединения
Резьбовыми называют соединения составных частей изделия с применением деталей, имеющих резьбу. Они наиболее распространены в приборо- и машиностроении. Резьбовые соединения бывают двух типов: соединения с помощью специальных резьбовых крепежных деталей (болтов, винтов, шпилек, гаек) и соединения свинчиванием соединяемых деталей, т.е. резьбы, нанесенной непосредственно на соединяемые детали.
Достоинствами резьбовых соединений являются простота, удобство сборки и разборки, широкая номенклатура, стандартизация и массовый характер производства крепежных резьбовых деталей, взаимозаменяемость, относительно невысокая стоимость и высокая надежность.
Недостатками резьбовых соединений являются наличие концентраций напряжений во впадинах резьбы, что снижает прочность соединений; чувствительность к вибрационным и ударным воздействиям, которые могут привести к самоотвинчиванию и низкая точность взаимоположения соединяемых деталей.
Основным элементом соединения является резьба, т.е. поверхность, которая образуется при винтовом движении плоской фигуры по цилиндрической или конической поверхности. Соответственно различают цилиндрическую и коническую резьбы.
По профилю выступа и канавки резьбы в плоскости осевого сечения резьбы делятся на треугольные, трапецеидальные симметричные, трапецеидальные несимметричные или упорные, прямоугольные и круглые.
По назначению резьбы разделяют на крепежные, крепежно-уплотнительные и ходовые.
Крепежные резьбы применяют для соединения деталей, а ходовые – в передаточных механизмах.
Крепежные резьбы имеют, как правило, треугольный профиль с притупленными вершинами и дном впадин. Это повышает прочность резьбы и стойкость инструмента при получении резьбы.
Крепежная резьба бывает метрической, дюймовой и трубной.
Наиболее широко применяется метрическая резьба. Угол профиля, т.е. угол между смежными боковыми сторонами резьбы в плоскости осевого сечения, метрической резьбы α = 60°.
Стандартом предусмотрена резьба с крупным и мелким шагом.
Резьбу с крупным шагом обозначают М (метрическая), при этом указывают значения наружного диаметра, например, М6, М8 и т. д. Для резьб с мелким шагом дополнительно указывают значение шага, например, М6×0,75, М8×1 и т.д.
Дюймовая резьба используется при замене деталей устройств, импортируемых из стран с дюймовой системой мер. Угол профиля дюймовой резьбы — α = 55°.
Основными крепежными деталями резьбовых соединений являются болты, винты, шпильки, гайки, шайбы и стопорные устройства, предохраняющие гайки от самоотвинчивания.
Рассмотрим каждое из них.
Болт – цилиндрический стержень с шестигранной головкой на одном конце и резьбой – на другом. Болты в соединении используют в комплекте с гайкой, при этом резьба в соединяемых деталях не используется (рис. 1, а).
Винты – цилиндрические стрежни с головкой на одном конце и резьбой – на другом. Винт ввертывается в резьбовое отверстие одной из скрепляемых деталей (рис. 1, б), головки винтов могут иметь различную форму (цилиндрическую, полукруглую и др.).
Шпилька – цилиндрический стержень с резьбой на обоих концах, одним концом она ввертывается в одну из скрепляемых деталей, а на другой ее конец навертывается гайка (рис. 1, в).
Соединения при помощи шпилек применяют в тех случаях, когда в одной из соединяемых деталей нельзя выполнить сквозное отверстие и материал этой детали (с резьбой) не обладает высокими прочностными свойствами (пластмасса, алюминиевые, магниевые сплавы). Поэтому применение винта при частой разборке и сборке соединения из-за малой прочности резьбы не рекомендуется. Шпилька же ввинчивается в деталь с резьбой малой прочности только один раз – при сборке, при последующих разборках и сборках будет свинчиваться только гайка.
Замечено, что шпильки из-за отсутствия головок и концентрации напряжений в местах сопряжения головки со стержнем всегда прочнее винтов тех же размеров при действии динамических и переменных нагрузок.
Гайки служат для соединения скрепляемых с помощью болта или шпильки деталей. Как и головки винтов, гайки могут иметь разнообразную форму.
Назначение шайб, подкладываемых под гайку, головку винта или болта, – предохранение поверхностей деталей от задира при затягивании, увеличение опорной поверхности и стопорение.
Болты, винты, гайки изготавливают из углеродистых и легированных сталей.
Крепежные детали общего применения изготавливаются чаще всего из стали марок Ст3, Ст4, Ст5 без последующей термообработки. Более ответственные детали изготавливаются из сталей 35, 45, 40Х, 40ХН с поверхностной или общей термообработкой.
Мелкие винты делают из латуни ЛС59-1, дюралюминия Д1, Д16.
Для защиты поверхности крепежных деталей от коррозии, придания им необходимого цвета применяют цинкование, хромирование, кадмирование.
Угол подъема винтовой линии резьбы (j = 1,5 … 2,5°) меньше угла трения в резьбовом соединении (r » 3°). Этим обеспечиваются условия самоторможения и предохранения от самоотвинчивания. Однако при вибрации, тряске, динамических и транспортных воздействиях наблюдаются ослабления резьбовых соединений, поэтому предусматривают их стопорение.
Для стопорения резьбовых соединений используют увеличение трения по поверхности контакта, пластическое деформирование, постановка резьбы на краску, лак, а также введение запирающих элементов — пружинных или стопорных шайб, специальных разрезных гаек с повышенным трением при стягивании, корончатых гаек, закрепленных шплинтом, отгибных шайб и т. п.
***
Штифтовые соединения
Штифтом называют цилиндрический или конический стержень, плотно вставляемый в отверстие двух соединяемых деталей. Применяют штифты для точного взаимного фиксирования деталей и для соединения деталей, передающих небольшие нагрузки. В зависимости от назначения штифты делят на установочные и крепежные.
По форме различают цилиндрические и конические штифты. По конструкции рабочей части штифты выполняют гладкими и просечными, т.е. с насеченными или выдавленными канавками, что не требует развертывания отверстия и создает надежное соединение, предохраняющее штифт от выпадения в процессе работы.
На рис. 2 приведены основные типы штифтов: цилиндрический (а), конический (б), конический разводной (в), цилиндрические, насеченные с конца (г) и посредине (д), и трубчатый пружинный (е).
Цилиндрические штифты удерживаются в отверстиях за счет натяга или силы трения. Для предупреждения выпадания цилиндрические штифты должны изготавливаться с большой точностью и высокой чистотой поверхности. Отверстия под крепежные штифты в соединяемых деталях сверлят и развертывают совместно, для чего детали временно скрепляют.
При многократной разборке и сборке нарушается характер посадки и соответственно точность соединения. Предохранение цилиндрических штифтов от выпадения осуществляют кернением концов штифта, развальцовкой краев штифта или специальными пружинящими предохранительными стандартными кольцами, изготовляемыми из проволоки (рис.2, ж).
Для удешевления соединения применяют насеченные и пружинные трубчатые штифты. Насеченные штифты не требуют точной обработки отверстий и отличаются повышенной прочностью сцепления с материалом детали, но менее точно фиксируют детали. Пружинные трубчатые разрезные штифты обеспечивают прочное соединение деталей, допускают повторные сборки и не требуют высокой точности обработки отверстий. Диаметр отверстия для такого штифта принимают на 15 … 20% меньше наружного диаметра штифта.
Цилиндрические штифты применяются и как установочные, обеспечивая точное взаиморасположение соединяемых деталей. Для повышения точности необходимо увеличение расстояния между штифтами. При этом соединение штифта со съемной деталью выполняют по переходной посадке (К7/h6; M7/h6), а соединение штифта с основной деталью (корпусом) выполняют по посадке с гарантированным натягом (U7/h6; S7/h6).
Конические штифты благодаря конусности 1:50 обеспечивают самоторможение при действии на них поперечных сил. Они допускают многократную постановку их в отверстие при сохранении точности взаимного расположения соединяемых деталей.
Изготовление конических штифтов и отверстий под них более сложно по сравнению с цилиндрическими штифтами. Для облегчения удаления штифта отверстие для него делают сквозным. Чтобы предохранить конические штифты от выпадения, применяют штифты с резьбой, с рассечением на конце (разводные), пружинные кольца.
Штифты изготавливают из сталей 45, А12, У8. При особых условиях работы соединения штифты могут изготавливаться из других материалов.
Главными недостатками штифтовых соединений являются значительное ослабление сечения вала отверстием под штифт и необходимость точной обработки этого отверстия во избежание изгиба штифта или его выпадения. Поэтому диаметр штифта d для вала диаметром dв задают из соотношения d Ј (0,2…0,25) dв, а затем при необходимости проверяют на сдвиг (срез).
***
Шпоночные соединения
Шпоночные соединения служат для передачи вращающего (крутящего) момента от вала к ступице насаженной на него детали (зубчатого колеса, шкива, муфты и др.) или наоборот – от ступицы к валу. Шпоночные соединения осуществляют с помощью вспомогательных деталей – шпонок, устанавливаемых в пазах между валом и ступицей.
Достоинствами шпоночных соединений являются простота, надежность конструкции, невысокая стоимость, удобство сборки и разборки.
Недостатки шпоночных соединений – ослабление вала и ступицы шпоночными пазами, неустойчивость положения шпонки в пазах (выворачивание шпонки) и трудность обеспечения взаимозаменяемости, повышенные требования к точности изготовления, отсутствие фиксации деталей в осевом направлении.
В приборостроении применяют в основном соединения призматическими (рис. 3, а), сегментными (рис. 3, б) и цилиндрическими (рис. 3, в) шпонками.
Клиновые шпонки в точных механизмах не применяют.
Конструкция и форма шпонки связаны с технологичностью изготовления пазов под шпонку. Пазы на валах фрезеруют, а в ступицах – прорезают протяжками.
Шпонки могут применять в качестве направляющих, обеспечивающих легкое перемещение деталей вдоль вала.
Нагрузку у шпонок воспринимают боковые поверхности, которые сопрягаются с пазами по соответствующим посадкам.
Призматическую шпонку с валом обычно соединяют по переходной посадке, а со ступицей – по посадке с зазором. Это препятствует перемещению шпонки вдоль вала и компенсирует с помощью зазора неточности размеров, формы и взаимного расположения пазов. Такой характер соединения обеспечивает достаточную точность центрирования вала и ступицы. В радиальном направлении предусматривается зазор.
Призматические шпонки имеют прямоугольное сечение, они могут быть с округленными, плоскими и смешанными торцами. Паз под шпонку на валу делают на глубину около 0,6 от ее высоты, а паз во втулке – на длину всей ступицы.
Ширина и высота шпонки определены ГОСТом и выбираются в зависимости от диаметра вала. Размеры высоты и ширины стандартных шпонок подобраны так, что прочность на сдвиг обеспечивается с избытком, и при необходимости проверку шпонок на прочность проводят на деформацию смятия.
Сегментные шпонки требуют более глубоких пазов в валах, что уменьшает их прочность. Их применяют в случае передачи незначительных усилий, работают они как призматические, но более удобны в изготовлении.
Цилиндрические шпонки чаще всего используют для закрепления деталей на конце вала. Отверстие для шпонки обрабатывают в соединяемых деталях (вал и ступица) совместно.
Шпонка устанавливается с натягом.
Шпоночные соединения применяют обычно при передаче значительных вращающих моментов при диаметре вала не менее 6 мм. В кинематических передачах и передачах с высоким требованием по точности рекомендуют использовать штифтовые соединения.
Шпонки изготавливают из среднеуглеродистых сталей 40, 45, Ст6.
***
Шлицевые соединения
Шлицевые соединения служат для передачи вращающего момента между валами и установленными на них деталями.
Шлицевое соединение можно условно представить как многошпоночное, шпонки которого выполнены вместе с валом. С помощью этого соединения можно обеспечить как подвижное (с осевым относительным перемещением), так и неподвижное скрепление деталей.
По сравнению со шпоночными шлицевые соединения имеют значительно большую нагрузочную способность, прочность валов, точность центрирования и направления ступиц в подвижных соединениях.
По форме поперечного сечения шлицев различают прямобочные (рис. 4, а), эвольвентные (рис. 4, б) и треугольные (рис. 4, в) шлицевые соединения. Наибольшее распространение получили прямобочные шлицевые соединения, выполненные с четным числом шлицев (6, 8, 10).
Центрирование возможно по наружному диаметру D, по внутреннему d и боковым поверхностям.
Центрирование по наружному диаметру рекомендуется для неподвижных соединений, по внутреннему диаметру – для подвижных соединений, по боковым граням – при больших передаваемых нагрузках и низкой точности соединения.
Эвольвентное шлицевое соединение (см. рис.) отличается от прямобочного повышенной точностью центрирования и прочностью. Центрирование осуществляют по боковым сторонам, реже – по наружному диаметру.
Соединение с треугольными шлицами (см. рис.) применяют для неподвижных соединений при небольших нагрузках и тонкостенных конструкциях. Число шлицев z = 20 … 70, углы впадин вала равны 60, 72 и 90°.
Центрирование осуществляют только по боковым граням.
***
Профильные соединения
Профильным называется разъемное соединение, у которого ступица насаживается на фасонную поверхность вала.
Простейшим таким соединением является соединение вала, имеющего на конце квадратные поперечные сечения с маховичком, рукояткой. Сторону квадрата рекомендуют принимать равной примерно 0,75 диаметра вала.
К профильным соединениям относят соединения вала со ступицей по овальному, например, трехгранному контуру (рис. 5, а), соединение на лыске (рис. 5, б).
Достоинствами таких соединений являются лучшее по сравнению со шпоночным центрирование и отсутствие концентраторов напряжений.
К недостаткам следует отнести сложность и трудоемкость, относительно высокую стоимость изготовления фасонных поверхностей.
***
Клеммовые соединения
Клеммовыми называют фрикционные соединения деталей с соосными цилиндрическими посадочными поверхностями, в которых требуемое радиальное давление (натяг) и фиксация за счет сил трения создаются путем деформации изгиба охватывающей детали затянутыми болтами (рис.6 , а, б).
Эти соединения применяют для передачи вращающего момента и осевой силы между валами, осями и призматическими деталями (рычагами, щеками сборных коленчатых валов, частями установочных колец и т. п.).
При проектировании соединения обычно требуется определить силу затяжки, обеспечивающую взаимную фиксацию деталей и передачу требуемого вращающего момента, а также оценить прочность болта (болтов) и охватывающей детали (клеммы).
В приближенном расчете можно принять, что контактные напряжения от затяжки равномерно распределены по поверхности контакта (как в соединении с натягом). Тогда средние контактные напряжения qн связаны со сдвигающей нагрузкой Q соотношением:
qн = kQ/fminπdl,
где: fmin — коэффициент трения; l — ширина линии охвата детали клеммой; πd — длина этой линии.
Если соединение имеет n болтов, затянутых силой F0, то условие равновесия клеммы (рис. 6, б) имеет вид:
nF0 = qнld.
Учитывая приведенные выше соотношения, получим:
F0 = kQ/πnf
Диаметр резьбы болта для обеспечения такой силы затяжки определяется по формуле:
d1 = √{4F0/π[σр]} (здесь и далее √ — знак квадратного корня),
где [σр] – допускаемое напряжение для материалов болта.
Оценку прочности клеммы можно выполнить путем расчета методом конечных элементов или по теории колец.
***
Классификация резьбовых соединений
Главная страница
- Страничка абитуриента
Дистанционное образование
- Группа ТО-81
- Группа М-81
- Группа ТО-71
Специальности
- Ветеринария
- Механизация сельского хозяйства
- Коммерция
- Техническое обслуживание и ремонт автотранспорта
Учебные дисциплины
- Инженерная графика
- МДК.01.01. «Устройство автомобилей»
- Карта раздела
- Общее устройство автомобиля
- Автомобильный двигатель
- Трансмиссия автомобиля
- Рулевое управление
- Тормозная система
- Подвеска
- Колеса
- Кузов
- Электрооборудование автомобиля
- Основы теории автомобиля
- Основы технической диагностики
- Основы гидравлики и теплотехники
- Метрология и стандартизация
- Сельскохозяйственные машины
- Основы агрономии
- Перевозка опасных грузов
- Материаловедение
- Менеджмент
- Техническая механика
- Советы дипломнику
Олимпиады и тесты
- «Инженерная графика»
- «Техническая механика»
- «Двигатель и его системы»
- «Шасси автомобиля»
- «Электрооборудование автомобиля»
Integrated Publishing — ваш источник военных спецификаций и образовательных публикаций
Администрация — Навыки, процедуры, обязанности и т. д. военного персонала
Продвижение —
Военный карьерный рост
книги и т. д.
Аэрограф/метеорология
— Метеорология
основы, физика атмосферы, атмосферные явления и др.
Руководства по аэрографии и метеорологии военно-морского флота
Автомобилестроение/Механика — Руководства по техническому обслуживанию автомобилей, механика дизельных и бензиновых двигателей, руководства по автомобильным деталям, руководства по деталям дизельных двигателей, руководства по деталям бензиновых двигателей и т. д.
Автомобильные аксессуары |
Перевозчик, персонал |
Дизельные генераторы |
Механика двигателя |
Фильтры |
Пожарные машины и оборудование |
Топливные насосы и хранение |
Газотурбинные генераторы |
Генераторы |
Обогреватели |
HMMWV (Хаммер/Хамви) |
и т.д…
Авиация — Принципы полетов,
авиастроение, авиационная техника, авиационные силовые установки, справочники по авиационным частям, справочники по авиационным частям и т. д.
Руководства по авиации ВМФ |
Авиационные аксессуары |
Общее техническое обслуживание авиации |
Руководства по эксплуатации вертолетов AH-Apache |
Руководства по эксплуатации вертолетов серии CH |
Руководства по эксплуатации вертолетов Chinook |
и т.д…
Боевой —
Служебная винтовка, пистолет
меткая стрельба, боевые маневры, органическое вспомогательное вооружение и т. д.
Химико-биологические, маски и оборудование |
Одежда и индивидуальное снаряжение |
Боевая инженерная машина |
и т.д…
Строительство —
Техническое администрирование,
планирование, оценка, планирование, планирование проекта, бетон, кирпичная кладка, тяжелый
строительство и др.
Руководства по строительству военно-морского флота |
Совокупность |
Асфальт |
Битумный корпус распределителя |
Мосты |
Ведро, Раскладушка |
Бульдозеры |
Компрессоры |
Обработчик контейнеров |
дробилка |
Самосвалы |
Землеройные машины |
Экскаваторы |
и т. д…
Дайвинг —
Руководства по водолазным работам и спасению различного снаряжения.
Чертежник —
Основы, методы, составление проекций, эскизов и т. д.
Электроника —
Руководства по обслуживанию электроники для базового ремонта и основ. Руководства по компьютерным компонентам, руководства по электронным компонентам, руководства по электрическим компонентам и т. д.
Кондиционер |
Усилители |
Антенны и мачты |
Аудио |
Батареи |
Компьютерное оборудование |
Электротехника (NEETS) (самая популярная) |
техник по электронике |
Электрооборудование |
Электронное общее испытательное оборудование |
Электронные счетчики |
и т.д…
Машиностроение —
Основы и методы черчения, составление проекций и эскизов, деревянное и легкокаркасное строительство и т. д.
Военно-морское машиностроение |
Армейская программа исследований прибрежных бухт |
и т. д…
Еда и кулинария —
Руководства по рецептам и оборудованию для приготовления пищи.
Логистика —
Логистические данные для миллионов различных деталей.
Математика —
Арифметика, элементарная алгебра,
предварительное исчисление, введение в вероятность и т. д.
Медицинские книги —
Анатомия, физиология, пациент
уход, оборудование для оказания первой помощи, фармация, токсикология и т. д.
Медицинские руководства военно-морского флота |
Агентство регистрации токсичных веществ и заболеваний
Военные спецификации
— Государственные спецификации MIL и другие сопутствующие материалы
Музыка
— Мажор и минор
масштабные действия, диатонические и недиатонические мелодии, паттерны такта,
и т.д.
Основы ядра —
Теории ядерной энергии,
химия, физика и т.
Справочники Министерства энергетики США
Фотография и журналистика
— Теория света,
оптические принципы, светочувствительные материалы, фотофильтры, копирование
редактирование, написание публикаций и т. д.
Руководства по фотографии и журналистике военно-морского флота |
Руководство по армейской фотографии, печати и журналистике
Религия —
Основные религии мира,
функции поддержки богослужений, свадьбы в часовне и т. д.
Соображения по выбору конкретного постоянного или разъемного соединения для конструкции машины.
Принцип модульности стал нормой в инженерном проектировании. Модульность означает, что инженерные системы, такие как машины, спроектированы как группа автономных, независимых частей, собранных вместе, чтобы сформировать окончательную сборку (машину) с помощью некоторого соединения или крепления.
Как заметил Слокум (2008): «Все механические вещи имеют структуру, и эта структура часто состоит из частей. Структурные соединения предназначены, по существу, для постоянного соединения частей друг с другом. Структурные интерфейсы предназначены для того, чтобы детали можно было легко присоединять и отсоединять. …» То, что он назвал структурными соединениями, представляет собой неразъемные соединения, выполненные с помощью таких процессов, как сварка, в то время как структурные интерфейсы подразумевают крепление с помощью крепежных деталей, таких как болты и гайки.
Модульная конструкция — это шаблон проектирования, основанный на идее автономных модульных компонентов, которые можно независимо создавать, легко настраивать и реконфигурировать в различных системах (Complexity Lab.com, 2018). В модульной конструкции мы создаем подкомпоненты, а затем используем некоторые соединения или крепежные детали, чтобы собрать вместе и объединить эти подсистемы, чтобы построить всю механическую систему как составную часть модулей. Преимущество этого заключается в повышении ремонтопригодности, поскольку любой неисправный модуль можно быстро заменить заведомо исправным без отключения всей машины.
Существуют различные способы формирования соединений и интерфейсов. Каждый из них имеет свой собственный набор эвристических правил, которые позволяют проектировщику быстро и консервативно разметить соединение. Механика различных суставов также хорошо изучена, поэтому детальное проектирование сустава может быть выполнено детерминистически (Slocum, 2008). Неразъемные соединения формируются с использованием таких процессов, как сварка, пайка (обычно называемая сплавлением) или склеивание. Временные соединения возникают в результате использования крепежных деталей.
Крепеж — это элементы машины, которые соединяют или соединяют различные части машины. Соединения могут быть постоянного типа или временного типа . К неразъемным соединениям относятся те, которые нельзя разделить или разобрать на отдельные элементы, не разрушив или не повредив их. Примерами неразъемных соединений являются сварные соединения, заклепочные соединения и т. д. К временным соединениям относятся те, в которых отдельные элементы сборки можно легко отделить, не разрушая и не повреждая их. Соединения, полученные с помощью гайки и болта, и шплинтовые соединения являются распространенными и широко используемыми примерами временных соединений (Khemani, 2008).
Существует множество видов соединений или соединений, которые можно создать. К ним относятся: сварные, болтовые, винтовые и резьбовые, штифтовые и заклепочные, с натягом и с клеем.
Engineering Clicks – онлайн-форум по проектированию машиностроения – содержит три важных правила при выборе постоянного или временного соединения, как показано ниже: Слияние.
ПРАВИЛО 2 – Механическое крепление и сплавление/плавление обычно создают более прочные и долговечные соединения, чем клеевое соединение (ИСКЛЮЧЕНИЕ – эпоксидные смолы и перманентные клеи, такие как «Crazy» Glue, могут создавать очень прочные, почти неразъемные соединения. Кроме того, клеи, используемые на подложки, такие как наклейки, создают связь, которая, скорее всего, разрушит наклейку при удалении).
ПРАВИЛО 3 – Для компонентов, требующих разборки для технического обслуживания или замены, обычно предпочтительнее использовать механическое крепление.
Как они напомнили нам: «выбор соответствующего процесса соединения для поставленной задачи требует должной осмотрительности со стороны инженера, чтобы гарантировать, что требования приложения будут выполнены и соединение не выйдет из строя».
Индивидуальные процессы соединения
Ниже приведены рекомендации по отдельным процессам соединения:
Сварные соединения
Сварные соединения выполняются путем сплавления материала с такими же или близкими свойствами с подложкой. Преимущество сварного соединения в том, что это постоянное и прочное соединение. Сварные соединения, однако, являются жесткими и поэтому не подходят там, где применение требует гибкости движения (например, бокового изгиба) или кручения между соединяемыми элементами. Например, крепление бороны к трактору с помощью сварки будет проблематичным по нескольким причинам: отцепка для крепления других орудий будет невозможна, возникающие при работе изгибы могут создавать значительные напряжения в соединении, вызывая его поломку. Кроме того, при выходе из строя бороны нет возможности быстро заменить новую борону в сборе в нормальных полевых условиях. Для этого потребуется вернуть трактор и борону в мастерскую, чтобы отшлифовать соединение и приварить новое. В сельской местности, где возможности для таких работ, как шлифовка и специальная сварка, в основном недоступны, это означает, что полевые работы будут заземлены.
Таким образом, сварные соединения плохо ремонтопригодны для соединений, требующих гибкости.
Преимущества сварных соединений можно резюмировать следующим образом:
- Относительно небольшой вес: Сварные конструкции обычно легче по весу по сравнению с клепаными конструкциями. Это связано с тем, что при сварке не используются косынки или другие соединительные элементы.
- Большая фиксация: Сварные соединения обеспечивают высокую эффективность, что невозможно в случае заклепочных соединений.
- Легче исправлять ошибки: Можно легко вносить изменения и дополнения в существующие структуры.
- Эстетика: Сварные конструкции имеют гладкий внешний вид, поэтому выглядят приятно. Сварные соединения выглядят лучше, чем громоздкие заклепочные/стыковые соединения.
- Однородность материала соединения и исходного материала: Сварное соединение обладает большой прочностью. Часто сварное соединение имеет прочность самого основного металла.
- Минимальное занимаемое место: Можно легко сварить любую часть конструкции в любой точке. Но другие процессы соединения, например. клепка требует достаточного зазора.
- Быстрее: Процесс выполнения сварных соединений занимает меньше времени, чем другие соединения. Скорость изготовления выше по сравнению с другими, например. заклепочные соединения.
- Экономичность: Сварные соединения более экономичны, так как требуют меньше труда и материалов.
- Можно применять для сварки нестандартной геометрии: Такие формы, как цилиндрические стальные трубы, легко свариваются.
Но их трудно клепать.
- Повышенная прочность: Сварка обеспечивает очень прочные соединения, которые нелегко согнуть. Полные жесткие соединения могут быть обеспечены с помощью сварки. Это соответствует современной тенденции создания жестких рам.
- Повышенная структурная целостность: Поскольку для сварки не требуется отверстие, следовательно, площадь не уменьшается. Таким образом, элементы конструкции более эффективно воспринимают нагрузку. Нет опасности изнашивания и проламывания крепежа через вмятину или отверстия, сделанные в основном материале. В сварных соединениях растянутые элементы не ослабляются, как в случае заклепочных соединений.
- Бесшумная работа: В процессе сварки не возникает шума, как при клепке.
Недостатки:
- Склонность к усталости: Сварные соединения более хрупкие, поэтому их усталостная прочность меньше, чем у соединяемых элементов.
- Введение напряжения из-за термического воздействия: Из-за неравномерного нагрева и охлаждения элементов во время сварки элементы могут деформироваться, что приводит к дополнительным напряжениям.
Так как в процессе сварки при изготовлении происходит неравномерный нагрев и охлаждение, то элементы могут деформироваться или возникать дополнительные напряжения.
- Требование к более высокому уровню квалификации: Для сварки требуются квалифицированная рабочая сила и электричество.
- Склонен к растрескиванию: В сварном соединении не допускается расширение и сжатие, поэтому существует вероятность образования трещин.
- Более сложная проверка качества: Проверка сварочных работ сложнее и дороже, чем в других процессах соединения. Такие дефекты, как внутренний воздушный карман, шлаковые включения и неполное проплавление, трудно обнаружить.
Сварные соединения часто используются в конструкциях рам навесного оборудования, таких как рамы дисковых плугов, окучников, культиваторов, скребков и т. д. Ключевым фактором при проектировании здесь является обеспечение жесткости рамы и большой устойчивости к изгибам и усталости.
Болтовые соединения
В них используются болты и гайки для соединения двух или более компонентов вместе. Болтовые соединения находят применение при соединении настила силоса, креплении компонентов машин (например, дисков, борон, колес и шкивов ременного привода и т. д.) к раме или валу, креплении ножей к измельчающему барабану зерноуборочного комбайна и т. д. Поскольку резьба эффективно фиксируется, они используются в качестве контргаек в гидравлическом оборудовании, таком как домкраты и другие подобные устройства, такие как приспособления и приспособления для зажимных колес, патронов и т. д., а также натяжители для ременного привода в промышленном оборудовании, комбайнах и ленточных конвейерах.
Например, диски плуга крепятся болтами и гайками к раме, а также автомобильные шины, рулевое управление и т.д.
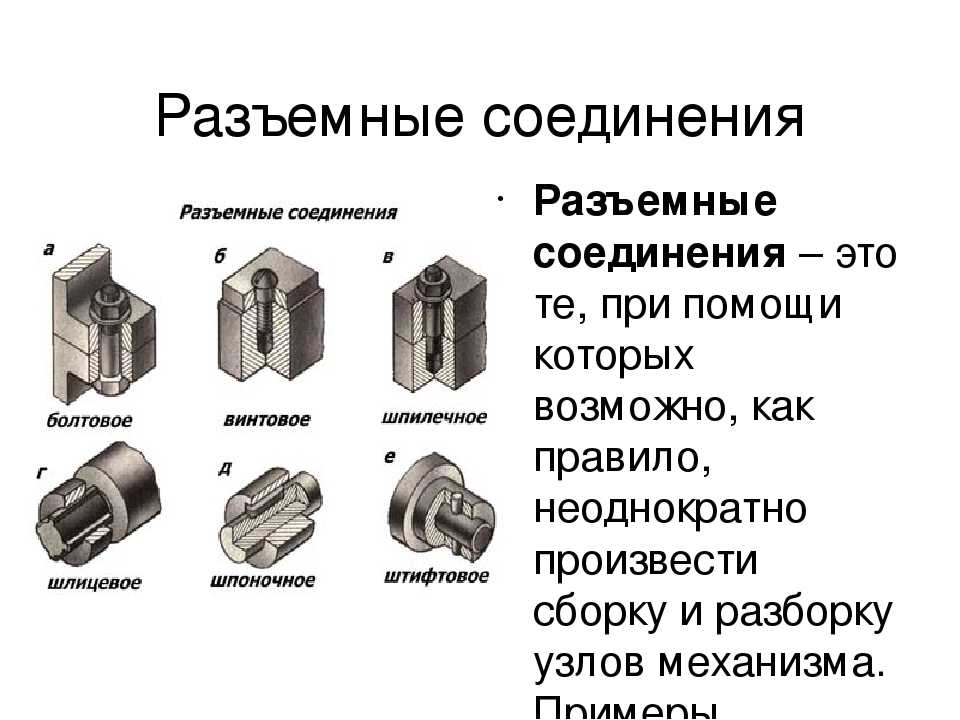
Недостатки
Хотя болтовые соединения популярны в конструкции машин, они создают некоторые проблемы.
- Склонность к сдвигу: Болты, подвергающиеся скручивающей или сдвигающей нагрузке, могут разрушиться быстрее, чем сварные швы.
- Коррозионно-фильный : Также они склонны к воздействию окружающей среды, где болты подвергаются воздействию воздуха и дождя; это приводит к коррозии, которая может привести к выходу из строя соединения. Для соединений класса А, отказ которых может привести к значительному повреждению оборудования или травмам человека, это нежелательно.
- Шум и дребезг во время обслуживания : При использовании болтов в качестве крепежа может увеличиться шум. В бесшумных операциях это большой недостаток.
- Резонансная усталость : Когда гайки ослабевают, болты, ставшие свободными, могут вибрировать и вибрировать, создавая резонанс, который может привести к поломке. Хочется надеяться, что при проектировании это было учтено и учтено.
- Разрушение : В машинах, где соединение болта и гайки подвергается сильному натяжению (растягивающему напряжению) и/или высоким температурам, они имеют тенденцию к расширению (или, наоборот, к усадке или сжатию).
Такое сжатие или расширение может изменить конфигурацию и/или функционирование соединения, что может неблагоприятно повлиять на работу машины.
- Плохое уплотнение жидкости : там, где требуется уплотнение жидкости в соединении, они могут протекать при износе резьбы. Жидкость часто просачивается через зазоры между болтами и гайками и зажимными элементами машины.
Резьбовое и резьбовое соединение
При резьбовом креплении две сопрягаемые части с наружной и внутренней резьбой соединяются друг с другом, образуя соединение. Эти соединения обеспечивали легкую разборку и ремонтопригодность. Они достаточно сильные. Их себестоимость почти такая же, как у болтов и гаек. Шурупы и специальные шестигранники особенно плотно прилегают к поверхностям, где требуется эстетичность и внешний вид аккуратной поверхности, например, к столешницам и приборным панелям оборудования.
Однако им не хватает прочности сварных соединений, и они подвержены воздействию окружающей среды, вызывающему коррозию.
Резьбовое соединение в основном используется для крепления элементов машин, рабочие условия которых не требуют несущей боковой нагрузки и/или напряжения сдвига. Так, например, заводские таблички оборудования могут быть привинчены сбоку к двигателю или навесному оборудованию.
Другие достоинства резьбовых соединений:
- Надежность: Резьбовые соединения отличаются высокой надежностью в эксплуатации.
- Быстрая установка: Резьбовые соединения легко монтируются и демонтируются.
- Огромное разнообразие и выбор: Доступен широкий ассортимент резьбовых соединений для различных условий работы.
- Доступность: Шурупы относительно дешевы.
- Пригоден для массового производства: Благодаря стандартизации можно применять дешевые производственные процессы.
- Передача Pro-power: Винты могут использоваться для передачи мощности, например ходовой винт, и в этом случае они работают как соединение болта и гайки.
Некоторые из их недостатков:
- Ослабление: Резьбовые соединения ослабевают из-за вибрации машины.
- Требуются дополнительные аксессуары в критических условиях: Поскольку в критических случаях они не должны ослабляться, добавляются дополнительные компоненты (фрикционные гайки, стопорные шайбы, крутящий момент, Loctite, деформированная резьба, проводка, штифты). Они увеличивают общий вес сборки.
- Износ резьбы: Резьба изнашивается из-за многократного ослабления и затягивания.
- Склонен к повреждению при установке из-за человеческой ошибки: Может быть поврежден во время установки из-за чрезмерного затягивания (требуется динамометрический ключ)
- Меньшая прочность: Требуется отверстие (что делает их потенциально менее прочными, чем сварка/пайка/склеивание в некоторых случаях). Таким образом, прочность резьбовых соединений несопоставима со сварными или заклепочными соединениями.
- Увеличенная общая полезная нагрузка: Может быть громоздким в некоторых приложениях (например, листовой металл) и, таким образом, увеличивать вес сборки.
- Концентрация напряжения, предрасполагающая к отказу: Концентрация напряжения в резьбовых частях изменяется в зависимости от различных условий.
Штифтовые и заклепочные соединения
Часто требуется просверлить отверстие, в которое с усилием вставляется штифт или заклепка. Штифтование особенно полезно в тех случаях, когда для соединения требуются незаметные, не выступающие соединители, как, например, в муфтах машинных валов. Хотя штифты плотно входят в такие соединения, они могут быть срезаны из-за высоких крутящих моментов, которым подвергаются некоторые узлы вращающихся валов. Штифты оказались популярными для соединения звеньев роликовых цепей. Заклепочные соединения также распространены в конструкциях для сшивания листов, используемых в животноводческих помещениях, капотах и крышках машин и кровельных покрытиях. Также они используются для соединения ленточных лент конвейеров комбайнов.
Преимущества заклепочных соединений:
- Устойчивость к вибрации: Заклепочное соединение более надежно, чем сварное, в приложениях, подверженных вибрации и ударным нагрузкам.
- Можно использовать для соединения менее прочных материалов: Заклепочные соединения можно использовать для цветных металлов, таких как алюминиевый сплав, медь, латунь, или даже неметаллов, таких как пластик и асбест.
- Меньшая термическая деформация: Заклепочные соединения не подвержены термическому последействию, поскольку в этом соединении не требуется нагрев.
- Менее обременительная проверка качества: Проверка качества в заклепочном соединении упрощается.
- Низкое повреждение основного элемента после демонтажа: При разборке заклепочного соединения соединенные компоненты повреждаются меньше, чем сварное соединение.
Недостатки заклепочного соединения:
- Более высокая стоимость материалов: Стоимость материала заклепочного соединения больше.
- Высокая потребность в рабочей силе: Затраты труда на заклепочные соединения также больше, чем на сварное соединение. Общая стоимость при использовании заклепочного соединения также высока.
- Относительно выше полезная нагрузка в сборе: Клепаная сборка имеет больший вес, чем сварная сборка.
- Шумные операции: Процесс клепки создает больше шума из-за ударов молотка.
- Концентрация напряжения: Отверстия, необходимые для установки заклепок, вызывают концентрацию напряжения.
- Более длительное время сборки: Время производства больше для сборки.
- Негерметичные соединения: Заклепочные соединения негерметичны и герметичны.
- Плохая эстетика: Выступ заклепочной головки отрицательно влияет на внешний вид заклепочной конструкции.